
At Emphysys, any project with a lot of electrical required prototyping through different stages. Custom built transformers, antennas, and other electrical technologies were a common occurence. I got to work on projects that involved this level of protoyping, from conceptual phase 0 to a completed piece of bench-top verified technology. One project that I got to work on in particular required a custom antenna to be made. The antenna was meant to facilitate wireless power transmission (WPT) over a distance. To make WPT work, your transmitter and reciever need to be purposefully designed, not only in physical shape and form, but even in material.
​
Working closely with the electrical engineers, I was tasked with creating a way to machine ferrite cores in house. Since we were in the early stages of the project, we had to prove the antenna would work before putting in orders for custom machined ferrite cores.
​
I learned about how ferrite is machined, and thought of ways to accomplish the same results in house, with equipment we had and for a fraction of the price.

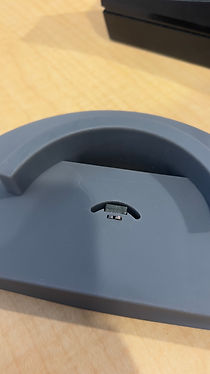
My first attempt at a jig is shown above. The curved wall meant to act as a physical stop to push a dremel up to. The dremel needed a specific cutting bit, diamond pattern carbide tipped steel. I though some small nyodinium magnets would do the trick at holding the ferrite core in place, but it proved unsuccessful. Keeping the ferrite core in place is difficult because it is a very brittle material, and requires little pressure to crack it. I designed a second iteration with a re-designed clamping mechanism, and sent it to the printer.



I ended up clamping the new rig, with the ferrite locked in, into a small container of water to provide cooling during the cutting process. I yielded an OK ferrite core with the desired dimensions, but I wasn't able to replicate this on the other half due to the way it clamped in. I needed a new method of securing and cutting the ferrite core.


I devised a way to use the Bridgeport CNC we had in the machine shop to help with the cutting, and make it a more passive process. After learning how to calibrate starting dimensions for the ferrite cutting sequence, I devised a tool path and plugged in all the information to the Bridgeport computer.
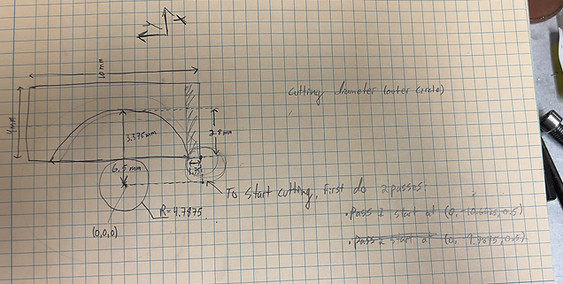
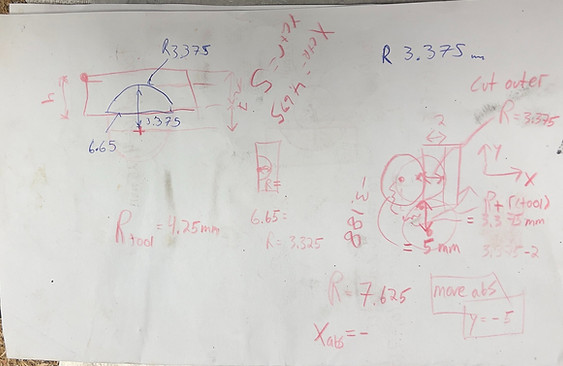

I devised a way to use the Bridgeport CNC we had in the machine shop to help with the cutting, and make it a more passive process. After learning how to calibrate starting dimensions for the ferrite cutting sequence, I devised a tool path and plugged in all the information to the Bridgeport computer.
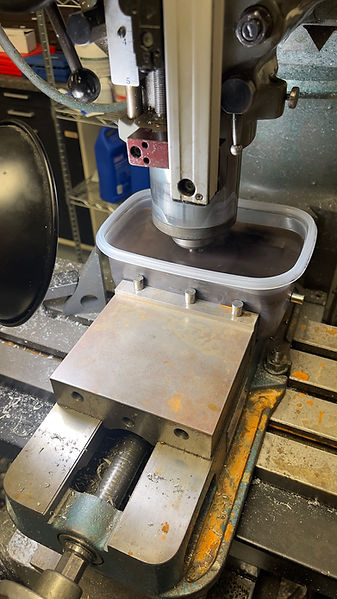

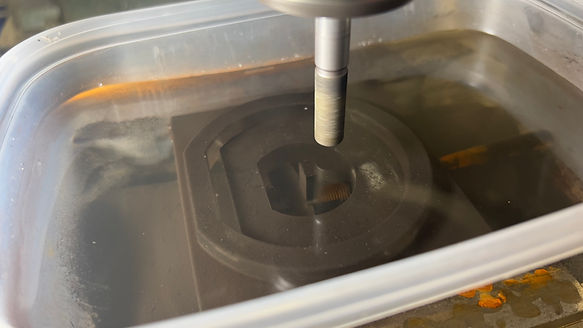


The final results were great, and allowed us to create a fully functional benchtop prototype using this ferrite core as one half of the antenna.