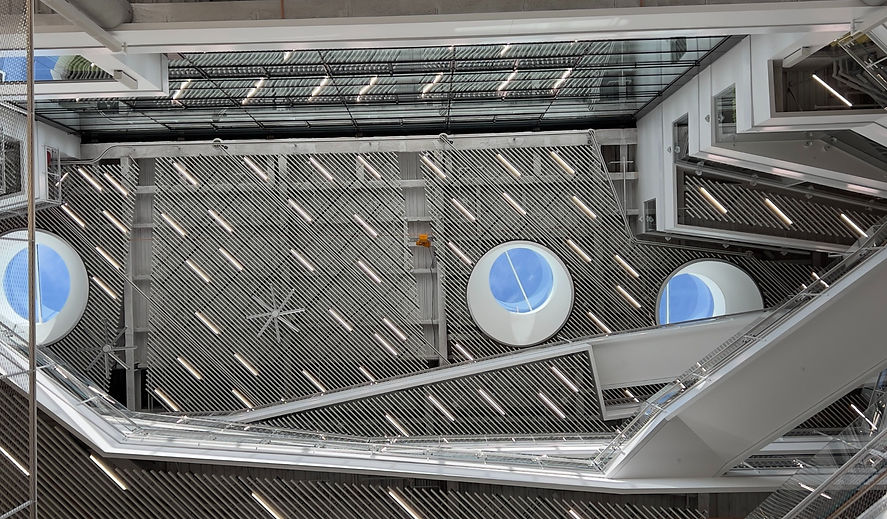
My friends and I formed a team and applied for the 2024 MakeHarvard event. We initially formed a team of 6, but with a change in the competition two days before commencement, we were forced to split into two teams of three. We met up the night before the competition and brainstormed a bunch of ideas for potential projects. Although we had to split into two teams for the competition, we did the brainstorm together. The initial ideas we came up with are listed and shown in the bottom left picture. The original idea we wanted to explore was a robot that could be used for gardening/agriculture. When we split into two teams, I came up with the idea for a smart storage system, inspired by the movie Wall-E. The sketches in the bottom right picture show the ideas we came up with for how to design it, and a short list of priorities and considerations is included.


Having participated in the MakeMIT event last year, we knew what type of materials we could expect to see, and wanted to utilize everything. We came up with an outline for workflow and knew loosely what materials we would have to use. We knew we would see materials like 80/20 aluminum rails, acrylic and wood panels (1/8-1/4 inch), stepper motors, Arduino boards and motor controllers, scrap wood, etc. because of their low cost and usability. On the morning of the competition, we met up around 7:30 in the morning and commuted over Harvard's Science and Engineering Complex, fueled by energy drinks and an excitement to build.


The first thing we did was build a simple frame, and slotted in some wood panels for a base and top. I designed shelving on Fusion 360, but the size was too large for the printers there, and even if I segmented it into multiple prints, it would take too long. Instead we decided to build some out of wood. It is not ideal, but under the time constraints, it was a good choice.
The video above shows the cutting of basic wood panels that we could use to construct walls for the shelves. We tested the assembly of our shelf unit with the walls placed, and finalized that as the design. The rest of the shelf walls were glued and set to dry over time.
​
With the shelves assembled we inserted a stepper motor to actuate the rotation of the unit (not sensing a potential problem which ended up appearing later). While the shelves were drying, I assisted with some electrical tasks, correcting the voltage boost on a converter, troubleshooting the actuation of the stepper motor, and learning how to wire it in accordance with the L298N H-bridge stepper motor driver.


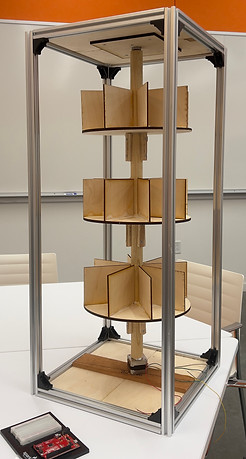
We got the structure complete, and just when we went to test the rotation of the shelves, the stepper motor stopped working. We already identified that the supply voltage and current were in the nominal operating range, so we coudln't have blown it out that way, and we deduced that it was an over-torque that fried the motor. The motor could not handle the rotation of the motor while holding it from below, and it exposed our poor decision choice.
​
At the time we tested this, the tool shop had closed, and we were not really able to do much. With limited time in the morning to finish the project, and still a long way to go, I came up with a quick solution to the problem. The basic idea of the solution was to leverage torque, and extend the lever arm of the rotation. So instead of spinning it from the center, I hammered in 4 equally spaced pulleys to the underside of the bottom shelf, and affixed a motor with another pulley to the frame, using zipties temporarily. We tested it and it worked! With the shelves now able to spin, we had a few other items to check off: mounting everything securely, getting the inventory system code working properly, and putting finishing touches on the exterior. The video on the bottom left shows us testing simple rotation, using the new method I devised. The middle image shows the bracket I made for the stepper motor, to keep it at the right height. We designed a motor bracket to use, but the print time close to 3 hours for 2, and we were in a rush. The bottom right video shows the system working with the newly secured stepper motor, and with the entire shelf system secured to the frame.

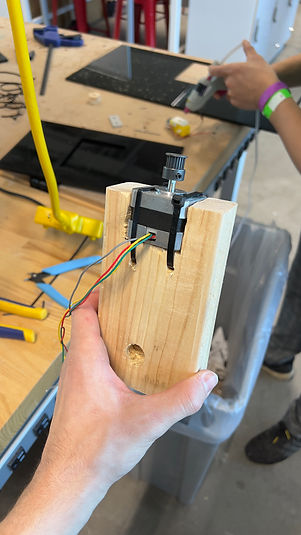
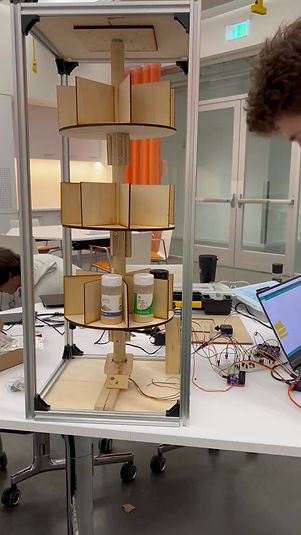
The images below show the final product. We fashioned some walls out of foam, and the walls with openings were made from laser cut black acrylic. The categories we were judged on were creativity, depth (problem and solution, technical difficulty, value to society, and usability. Our automated spice rack served to solve the problem of looking for spices, making the cooking process easier. Voice automated, our solution scored high on usability and depth. I have never seen something like this on the market, and got the idea from an animated movie, so I think we did well for creativity also. In terms of technical difficulty, this project entailed the design and integration of mechanical, electrical, and software solutions, which our team of 3 was able to navigate in just a 15 hour building window. We ended up winning Best MakeHarvard Original award for our project.


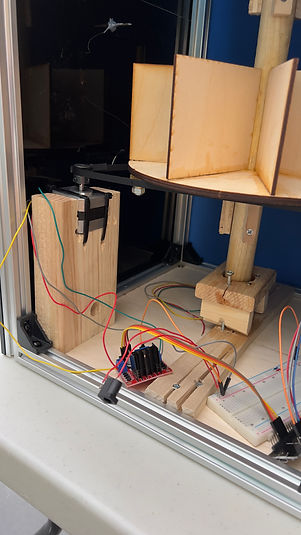
The media below are just extra tidbits from the competition. On the left shows these cool kinetic art pieces they had in the lobby of their building. The middle video shows a simple rack and pinion sliding door mechanism that we would've been able to implement, given just a little more time, but didn't make the presentation. The last picture is all of us after the competition, all running on under 5 hours of sleep.


